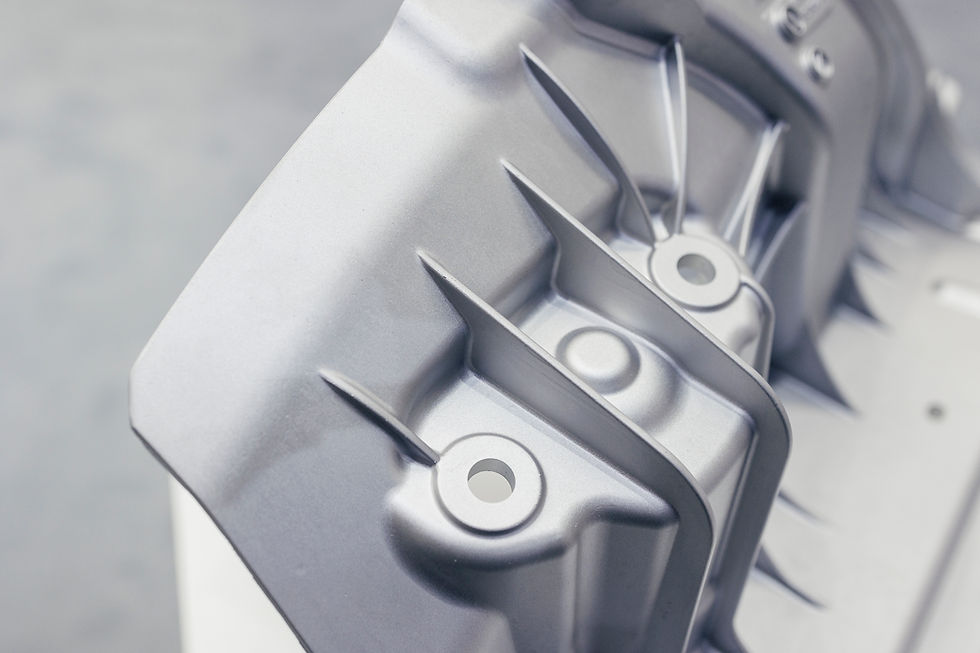
The place to be for professionals related to die casting
5 reasons not to miss it:
#1 Networking Opportunities: Connect with a diverse array of professionals, from industry leaders to technical experts and
decision-makers including the overall foundry industry represented at the co-located partner event Global Foundry Show.
#2 Market Insights: Gain valuable market intelligence about the Latin American region, a growing hub for industrial manufacturing.
#3 Product Comparisons: Evaluate a wide range of products and services from leading suppliers all in one place. Compare features, specifications, and pricing to make informed purchasing decisions for your business.
#4 Knowledge Enhancement: Participate in a dynamic conference program featuring keynote speakers. Gain insights into emerging trends, best practices, and future developments shaping the die casting sector.
#5 Hands-On Demonstrations: Engage directly with exhibitors to understand product capabilities and explore potential applications for your business.
Discover EUROGUSS MEXICO
EUROGUSS MEXICO successfully transfers its highly specialized and globally established event concept to the Mexican, Latin- and North-American market. The entire manufacturing chain of die casting is on display.



Melting furnaces are indispensable elements in the die casting process. They enable the precise melting of casting materials and alloys, which in turn form the basis for high-quality products. Advances in technology have led to improved energy efficiency and precise temperature control. At the same time, melting furnaces contribute to sustainability by promoting the recycling of metals and reducing the use of primary resources. In an increasingly resource-conscious world, melting furnaces thus play a crucial role in the production of high-quality products.
Step 1: Melting and raw materials
Overall, melting furnaces are indispensable components of the die casting process. They enable the precise melting of casting materials and alloys - the basis of high-quality products.


Precision is crucial in the die casting industry, so quality assurance and control play an important role. To ensure that the castings produced meet the highest quality standards, modern testing methods such as X-ray, ultrasound and non-destructive testing are used. The use of sophisticated measurement technology ensures accurate monitoring of dimensional accuracy and surface finish.
Step 4: Quality assurance
Precision is essential in the die casting industry, which is why quality assurance and quality control play a major role.

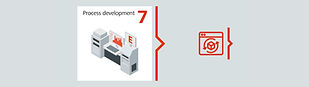
Process planning and development in die casting are crucial for the manufacture of high-quality products. The use of state-of-the-art software, the integration of Industry 4.0 concepts and continuous research and development are keys to increasing efficiency and quality. This will lead the industry into a promising future.
Step 7: Process development
Efficiency and quality through process planning and development in die casting. Industry 4.0 concepts and research are key to the industry's promising future.


The die casting process is a complex interplay of technology, precision and efficiency. From the sophisticated die-casting machine to the automated periphery to the precise tooling and optimised use of operating materials - every detail contributes to the production of high-quality metal parts. With a focus on sustainability and advancing technology, the die casting process remains a cornerstone of modern manufacturing, constantly evolving to meet industry demands.
Step 2: Die casting process
The die casting process is a complex combination of technology, precision and efficiency. Every detail plays an important role in the production of high quality metal parts.


The further processing of castings in die casting is a key process that ensures quality and functionality. By integrating innovative technologies and environmentally friendly practices, companies can not only produce high quality products but also contribute to sustainability. This helps to shape a better future for the industry and the environment.
Step 5: Further processing of castings
Machining of castings is essential in the process of die casting, which optimizes the quality and functionality of the produced parts.


Heat treatment and finishing of castings in the die-casting process are crucial steps to maximise the quality and performance of metal parts. By using modern furnaces, high-quality peripheral equipment and environmentally friendly practices, companies can not only produce first-class products but also fulfil their environmental responsibilities. The combination of quality and sustainability is key to the successful production of die-cast parts.
Step 3: Heat treatment and casting post-treatment
Important steps in improving the quality and performance of metal parts include heat treatment and post-processing of die castings.

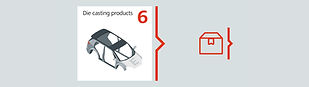
The wide application of die cast products in various industries illustrates their versatility and performance. From automotive to aerospace, medical to agriculture and more, die-cast products offer customised solutions that meet the demanding requirements of different industries. Thanks to advancing technologies and continuous innovation, die-cast products will continue to play a key role in the modern manufacturing landscape.
Step 6: Die-cast products
The high demand for die castings is due to their versatile properties, especially their strength and precision.
Product groups of
EUROGUSS MEXICO
-
FoundriesAluminium die casting parts Magnesium die casting parts Zinc die casting parts Die casting parts from other alloys Low pressure die casting parts Thixomolding casting parts Casting parts in other processes and materials
-
Casting machines and equipmentsDie casting machines cold chamber Die casting machines hot chamber Thixocasting machines Thixomolding machines Low pressure casting machines Other casting machines Complete casting cells Used machines trade Spare parts and accessories for casting machines
-
Periphery and aftertreatmentDosing and feeding equipment for molten metal Rheocasting Casting chamber, casting flasks and accessories Temperature control equipment for tools and casting machines Release agent spraying systems and equipment Vacuum technology Extraction equipment and robots Quenching and cooling of castings Punching and deburring technology Straightening Cleaning technology and equipment Mechanical processing of castings Surface treatment and finishing Core shooters Casting identification e.g. barcode, DataMatrixCode, etc. Conveying technology
-
Furnace and furnace accessoriesMelting furnaces Holding furnaces Dosing furnaces Heat treatment furnaces Process heat technology Melt treatment and purification Crucibles for melting and holding furnaces General accessories for melting and holding furnaces Refractory materials and components
-
Molds and tool makingDie casting tools Low pressure casting tools Mold development and design Molding materials Standards and accessories for mold making Tools for core shooting Heating elements for toolmaking Machining and machining centers for tooling Spotting presses Cleaning technology for molds and tools Additive manufacturing for tool inserts and accessories
-
Casting materials and alloysAluminium Magnesium Zinc Copper, brass, bronze Other casting materials
-
Operating materials and consumablesRelease agents for die casting molds Release agents and lubricants Coatings Tempering media Hydraulic media Corrosion protection Heat treatment and quenching media Molding materials, mold cores, core packages
-
Joining and connecting technology for castingsWelding Riveting Mechanical joining Gluing Other joining and connecting techniques
-
Sand casting, machine mouldingFlask moulding Flaskless moulding Lost foam process Vacuum sand casting Shell moulding Core package process Special processes
-
Sand casting machines and casting equipmentCasting equipment, mechanical Casting equipment, dosing Casting equipment, heated Pouring ladles Launders Pig casting machines Precesion fine casting units Special processes Accessories, operating and auxiliary material
-
Mould and core production for sand and gravity die castingMoulds and patterns Foam patterns Plastic patterns and core boxes Wooden patterns and core boxes Metal patterns and core boxes Pattern plates Miscellaneous
-
Gravity die castingTilt pouring process Low-pressure die casting Gravity die casting Differential die casting method Special process
-
Gravitiy die casting machines and accessoriesGravity die casting machines Low pressure die casting machines Differential die casting machines Accessories, operating and auxiliary material
-
Deburring, separating, cleaning for sand and gravity die castingsDeburring machines Casting separating machines and equipment Sawing equipment Grinding machines and plants Cleaning rooms Cleaning tools Equipment for testing raw castings
-
Quality assurance and controlOptical component testing Endoscopy Tactile component testing X-ray inspection and computed tomography Ultrasonic testing Crack testing Thermal imaging Leak testing Weighing equipment Materials testing Defect and damage analysis Laboratory technology and general measuring equipment for quality inspection Quality management systems
-
Digitalization and Industry 4.0Automation technology Technology for data acquisition e.g. sensor technology Data evaluation and artificial intelligence Process control technology Control and regulation systems Process visualization systems Industrial networks, IoT
-
Additive ManufacturingProduction of additively manufactured metal parts Production of additively manufactured cores and molding materials Equipment for additive manufacturing of metallic materials Equipment for additive manufacturing of cores and molding materials Additive Manufacturing Software Additive manufacturing materials
-
Other service and consultingFactory and plant planning System and component development Process development and optimization Simulation service Production of casting prototypes Maintenance, repair and overhaul of casting machines
-
Environmental technology, recycling, sustainabilityEnergy management Life cycle assessment and CO2 balancing Extraction and filter technology Wastewater treatment Cooling water treatment Residual material recycling
-
SoftwareCasting process simulation Material simulation Structural-mechanical simulation Quality analysis and documentation CAD, CAE, CAM, CAQ, CNC, etc. Process planning Production control Product data management Supply chain management
-
Research and developmentUniversities and Chairs Non-university research institutions Industrial research service providers
-
Professional information and literature, associations, continuing educationAssociations and industry representatives Databases for technology and business Technical literature Trade journals Education and training